Advanced Oxidation Processes (AOPs), such as the electro-Fenton (EF) process, are widely used in wastewater treatment to remove environmental contaminants. AOPs eliminate contaminants via oxidation. In the electro-Fenton process, hydrogen peroxide is continuously produced at the cathode, then catalyzed into highly oxidative hydroxyl radicals. Chemical reactions involving these hydroxyl radicals result in the oxidation of the contaminants, making the EF process an effective technology for reducing concentrations of contaminants such as trichloroethylene in drinking water.
As the precursor of hydroxyl radicals, electro generation of hydrogen peroxide is an important step for the EF process. However, most hydrogen peroxide generation methods require an external oxygen supply, which is costly and highly inefficient. The utilization efficiency is usually lower than 0.1%, which limits the potential for scaling up the technology. Researchers in PROTECT Project 4 has developed a system that doesn’t require an external oxygen source. In a paper recently published in Electrochemistry Communications, Project 4 researchers presented the results of a study looking at methods for using anodic oxygen for the in-situ electro generation of hydrogen peroxide.
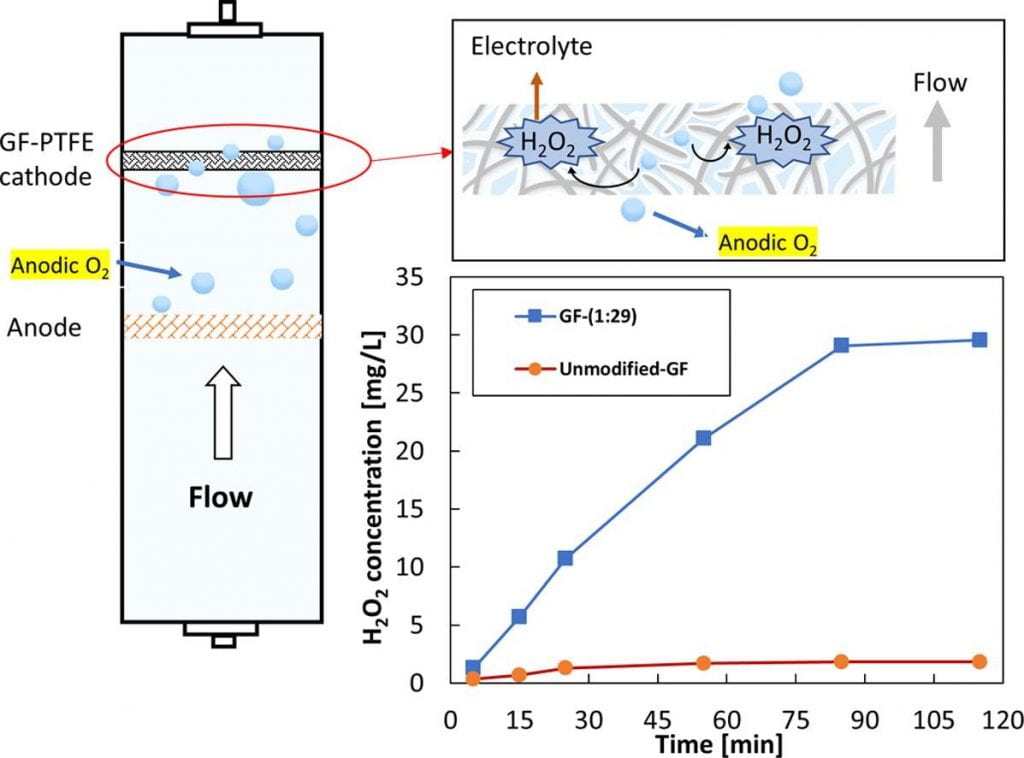
Graphical abstract
Optimizing conditions and cathode materials is key to improving the hydrogen peroxide production. For this study, researchers applied polytetrafluoroethylene (PTFE) to graphite felt (GF) to create a modified GF-PTFE cathode. To determine the ideal ratio of PTFE to GF, the team conducted tests with different quantities of PTFE applied to the graphite felt. The team also tested the efficacy of the GF-PTFE cathode under different flow rates, applied currents, and water pH conditions, and compared these results against an unmodified control cathode.
Researchers found that the GF-PTFE cathode produced 16 times more hydrogen peroxide than the control, and identified the optimal ratio of PTFE to the area of the GF electrode (1:29). The system was most effective at a flow rate of 3 mL/min and 120 mA in alkaline or neutral water; higher flow rates and more acidic water reduced efficacy. These promising results indicate that flow-through system is more efficient and cost-effective than systems that require an external oxygen source.
This work is an important step in PROTECT’s goal of developing a low-cost, environmentally-friendly, and low-maintenance device for remediating water contamination at the point of use. Because environmental contamination disproportionately impacts low-income communities, the cost efficiency of this device is key. The research team’s next steps will include assessing the efficacy of this system at degrading organic pollutants.